The True Cost of Equipment Downtime
Posted on February 20, 2024 by Boston Centerless
Equipment downtime is expensive no matter what industry you are in. The following article explores the true cost of equipment downtime and some ways Boston Centerless precision ground bar helps you reduce the financial and other forms of risk associated with unplanned downtimes.
A survey was recently conducted by Siemens entitled True Cost Of Downtime. One interesting finding is that in every sector surveyed, an hour of unplanned downtime costs at least 50% more now than it did a mere two years ago; the study attributed this to increasing inflation, stressed supply chains, and manufacturing facilities operating at higher capacities. So even though a company may have reduced the frequency or duration of unplanned downtimes in recent years, the overall financial burden caused by downtimes is likely still significant. For example, the survey indicated that just one hour of unplanned downtime in an automotive facility can cost more than $2 million USD. In addition to productivity losses that negatively impact the bottom line, unplanned equipment downtimes can also damage a company’s brand reputation and potentially cause loss of customers. Simply put, equipment downtime is costly.
The Relationship Between Equipment Downtime and TCO
Total Cost of Ownership (TCO) is the cost of owning a machine over its lifespan; TCO is broader and more encompassing than simply the initial price paid for a given machine. It is crucial that companies understand TCO in order to optimize cash flow as well as capital and expense funds management. TCO is comprised of two main cost categories: the costs associated with purchasing a piece of equipment and the costs associated with operating and maintaining the machinery through its life cycle. The operating and maintenance cost for a piece of equipment is where assumptions are made for maintenance intervals and durations and it is important to include the impact on production during the equipment downtimes for maintenance activities (i.e., lost production cost). There are also cost assumptions that must be factored in for unplanned downtimes as well.
Equipment downtime is simply any period of time when a machine is not in production. It is important to note that all downtimes are not created equal and unplanned downtimes are typically much more costly – and are often more expensive than anticipated. As visible as downtimes typically are, most companies underestimate the true cost of equipment downtime on the bottom line. Even a few hours of inactivity can cost millions of dollars, not to mention the production setbacks, supply chain headaches, and loss of customer trust you may also experience. The relationship between equipment downtime and TCO is simple – equipment downtimes drive up TCO. As with most aspects of manufacturing, an ounce of prevention is worth at least a pound of cure; thus, it is typically best to do whatever is possible to keep equipment up and running.
How Boston Centerless’ Precision Ground Bar Helps Reduce Equipment Downtime
When it comes to precision machining, the team at Boston Centerless knows that quality materials matter. In our experience, a higher investment in precision ground bar upfront yields a lower, overall TCO. At Boston Centerless, our skilled material yields bar stock that is superior than the competition. Our material is incredibly round and straight without inclusions – and we deliver unparalleled consistency and uniformity across our precision ground bar. These improved physical attributes translate to better CNC Swiss machining operations, namely less unplanned downtimes and a lower over equipment TCO.
Our team created the idea of Skilled Material, which is a concept that encompasses many facets of raw material properties, manufacturing processing and industry know-how to optimize your CNC Swiss operations – while reducing your overall cost of production. Our precision ground bar enables operators to run multiple Swiss machines at once - or even unattended - offering the opportunity for lights-out manufacturing without concern for quality issues. In addition, due to less vibration and wear on the machine, the use of precision ground bar leads to increased equipment and tool life as well as increased uptime – and an overall higher OEE. In short, Skilled Material improves equipment health and productivity while resolving bottlenecks, enabling businesses to grow. Skilled Material is a unique offering at Boston Centerless and is not available at most other suppliers – another reason that makes us a preferred precision machining partner across the globe. In addition, our skilled material enables lights-out manufacturing and ultimately lowers equipment TCO as well as the total cost of CNC Swiss operations. For these reasons, it is crucial that OEMs consider TCO and the true cost of equipment downtime into purchasing decisions for machinery and materials.
Would your project benefit from the reliability and manufacturability of Boston Centerless' precision ground bar?
Contact our team today to learn more about the operational benefits our precision ground bar provides and the reduction in equipment downtime our products often yield.
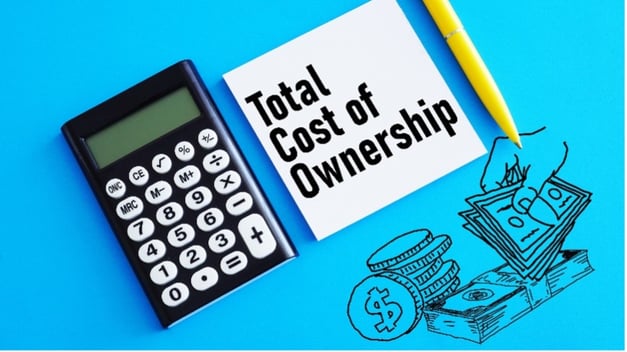
About Boston Centerless
Boston Centerless provides solutions that enhance our customers' manufacturing processes. With over 65 years of experience with precision grinding, we grind the tightest tolerances in the industry. We have proven experience with an extensive range of materials, and our manufacturing solutions include:
- AccuRod® Precision Bar
- BC Medical Grade
- Grinding Services
- Value-Added Services
- Material Testing & Validation
- Supply Chain Management
- SwissAssist
Contact us today at (781) 994-5000 to see how we can help with your next precision bar material project, or click here for a quote.