Aluminum: An Integral Element in Aerospace
Posted on January 25, 2024 by Boston Centerless
The aerospace sector has long relied on aluminum for its outstanding properties such as low density, corrosion resistance, and strength. In fact, it is believed that the Wright Brothers utilized aluminum parts in their first plane. In the decades that followed, aluminum continued to be an integral element in the aerospace industry as aircraft technologies advanced, enabling more fuel efficiency and speed while maintaining safety and comfort for passengers.
Today, aluminum alloys are used extensively across a variety of aerospace applications including engines, propellers, fuselage frames, fuel tanks, wings, pipes, seats, doors, floors, turbines, and rudders. Aluminum parts are present in a range of commercial, military, and cargo aircraft as well as NASA spacecraft and space shuttles. At Boston Centerless, we offer a range of aluminum alloys to serve the aerospace industry. We also offer a range of tools to help our customers select the material that is best for their specific application.
Aluminum Properties that Deliver for Aerospace
The aerospace sector demands absolute reliability in every aircraft component they manufacture, and this industry knows aluminum is dependable even amidst some of the harshest conditions on Earth – and beyond. Below are several key characteristics that make aluminum an excellent choice for aerospace applications.
- Incredibly Low Density (Light Weight): aluminum has a very low density compared to other metals which enables a superb strength-to-weight ratio. For this reason, aluminum alloys are used in applications where a combination of light weight and good strength are necessary. Due to its low density, the aerospace sector is able to utilize aluminum to reduce the weight of aircraft without sacrificing structural integrity and strength. Lower weights lead to improved fuel efficiency and longer flight capabilities – delivering significant cost benefits.
- Excellent Corrosion Resistance: aluminum naturally generates a thin oxide coating which protects the metal from coming in contact with moisture and other elements, resulting in excellent resistance to corrosion. This property increases the longevity of aluminum components when compared to other metals, and reduces the potential for weak points or failures in the field caused by corrosion issues.
- Outstanding Strength at Extreme Low Temperatures: like most properties, the strength of aluminum depends on the specific alloy but some aluminum alloys are quite strong. While some metals, such as steel, become brittle when exposed to low temperatures, aluminum is able to maintain its strength and, in some cases, even demonstrates increased tensile strengthas temperatures drop, which is a crucial property for some aerospace applications.
- Ease of Manufacturability: some metals are easier to fabricate than others and aluminum is able to be machined and formed via a variety of methods including forging, extrusion, rolling, and casting – offering manufacturing companies a range of options.
- Exceptional Longevity and Cost-Effectiveness: aluminum components are durable and proven to last decades across a range of applications. This long life cycle makes aluminum a cost-effective solution for the aerospace sector.
Would your next aerospace project benefit from the excellent strength, low density, and corrosion resistance that aluminum delivers?
Contact Boston Centerless today to learn more about how we serve the aerospace sector and our range of aluminum and other precision ground bar materials.
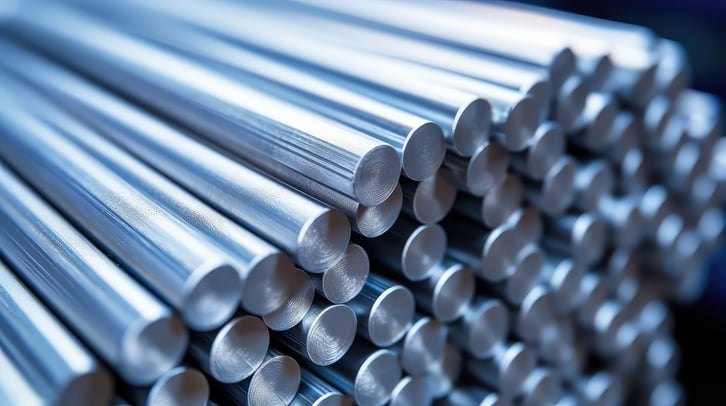
Aluminum Offerings at Boston Centerless
At Boston Centerless, we are committed to the high standards required by the aerospace industry and are Nadcap Accredited (NDT), AS9100 Certified, and ITAR Registered. The aluminum we source is of excellent quality and able to meet the stringent requirements of the aerospace sector.
At Boston Centerless, we supply precision bar materials and pre-production blanks for your machining needs. We can precision grind material to your exact specifications from our extensive inventory. If we do not have the material you need in stock, our team has a strong network with established long-term relationships with various mills and material suppliers. We are committed to providing reliable precision materials and only buy materials from the US or EU to ensure the material quality meets our standards. The high-grade materials that Boston Centerless procures combined with our precision grinding capabilities will ultimately reduce your manufacturing costs. The extremely precise straightness and roundness of precision ground AccuRod® bar enables increased feeds and speeds, as well as longer tool life, resulting in lower per part cost.
Boston Centerless offers the following aluminum materials:
1100 Series (All Tempers) | 6061 -T651 |
2011 Series (All Tempers) | 6061 -T6511 |
2017 -T4 | 7075 -T6 |
2017 -T451 | 7075 -T651 |
2024 Series (All Tempers) | 7075 -T6511 |
6061 -T6 |
|
Boston Centerless provides solutions that enhance our customers' manufacturing processes. With over 65 years of experience with precision grinding, we grind the tightest tolerances in the industry. We have proven experience with an extensive range of materials, and our manufacturing solutions include:
- AccuRod® Precision Bar
- BC Medical Grade
- Grinding Services
- Value-Added Services
- Material Testing & Validation
- Supply Chain Management
- SwissAssist
Contact us today at (781) 994-5000 to see how we can help with your next precision bar material project, or click here for a quote.